NEWS – 2023
28.12.2023
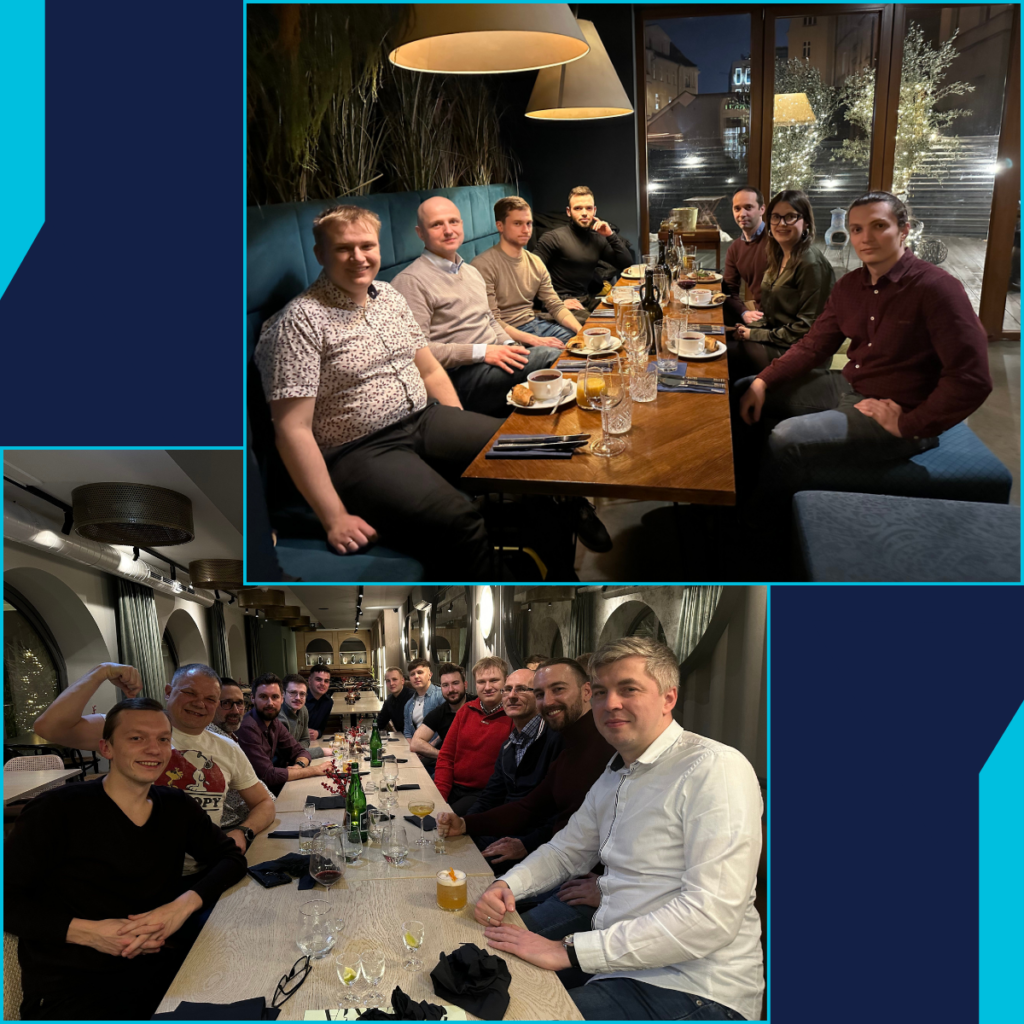
During the Christmas season, we had a chance to celebrate and have some quality time together at the festive meetings.
We had a great evening filled with delicious food and drinks, as well as interesting conversations. Christmas and New Year’s Eve season is the time for us to slow down and enjoy the moment, waiting for an upcoming year of 2024, for which we are ready 🙂
Merry Christmas and Happy New Year!
20.12.2023
During this holiday season, we would like to send our warmest wishes to you. May this Christmas bring you a lot of joy, peace and memorable moments spent with your loved ones.
We wish that the coming year of 2024 will bring you even more success, fulfilled goals and joyful moments in both your professional and private lives.
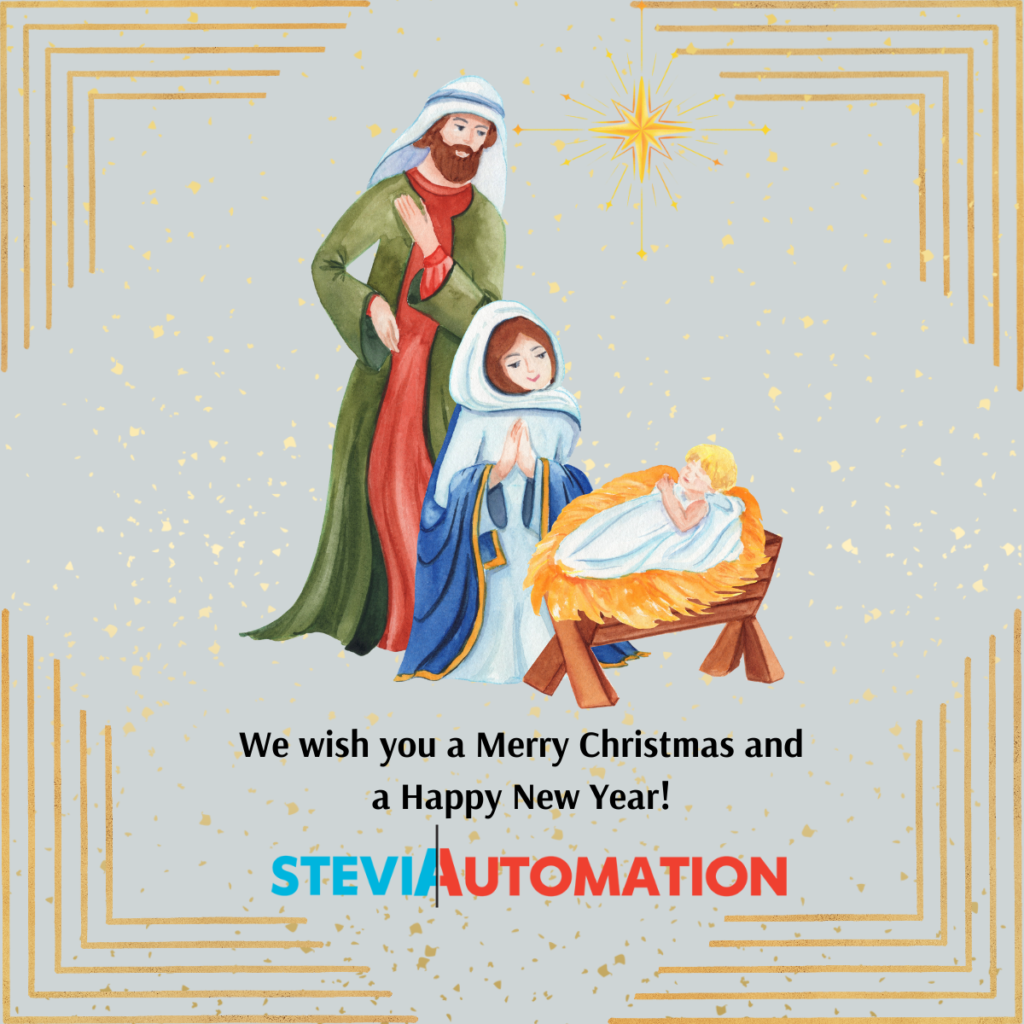
Happening this week: “Engineer of XXI century” Conference!
05.12.2023
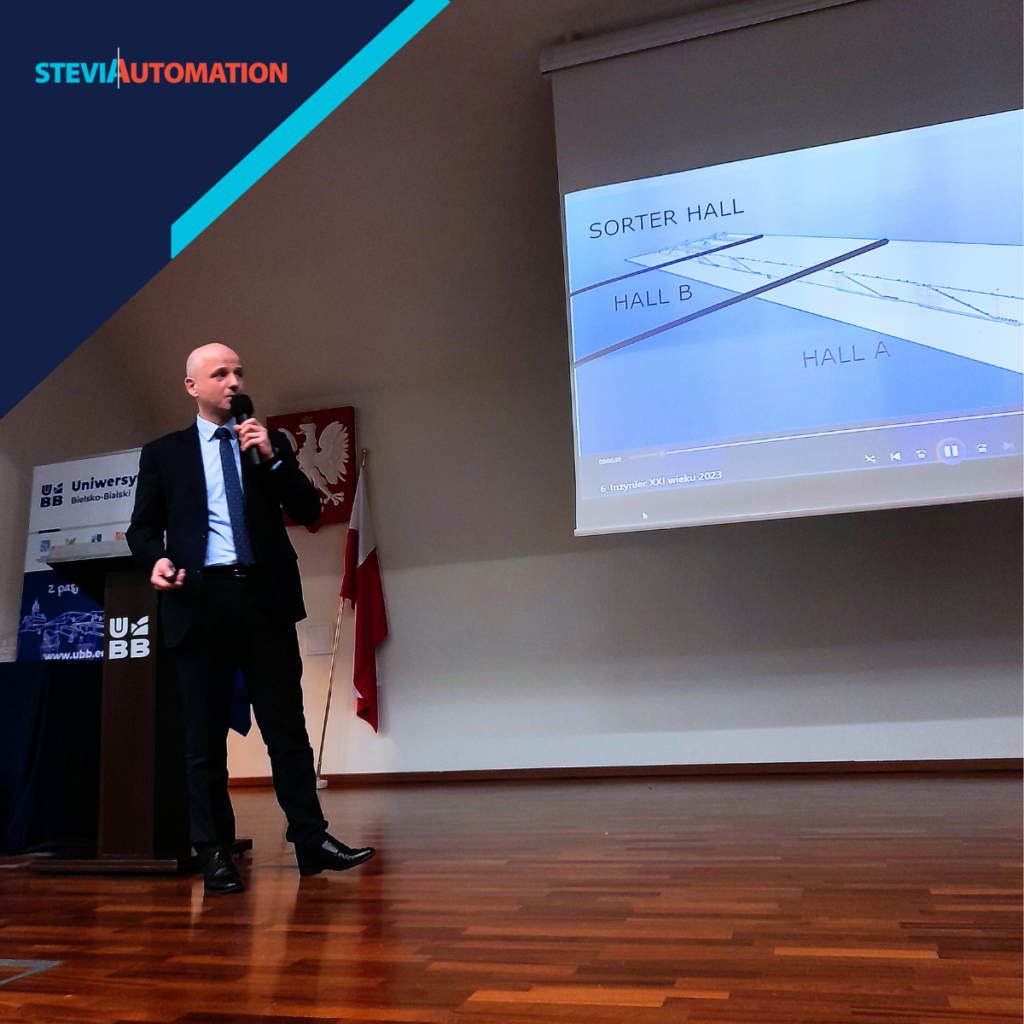
Last Friday, our team participated in the XIII International Conference “Engineer of XXI century” at University of Bielsko-Biała
We had a great time listening to inspiring speeches, exchanging opinions with other participants, and talking to students about our daily activities.
Our Managing Director, Paweł Wróbel, gave a speech about the impact of virtual reality on automation commissioning, which was a success and gained the attention of gathered students.
We are happy that we can collaborate with UBB University, as we can share our knowledge with the young generation, and get inspired by experts we met. Thank you to Uniwersytet Bielsko Bialski for the invitation!
Happening this week: “Engineer of XXI century” Conference!
05.12.2023
We are thrilled to be yet again a part of “Engineer of XXI century” conference, which will take place this Friday, 8th of December 2023, at University of Bielsko-Biała.
The event is organized by the “Engineer of XXI Century” Interdisciplinary Student Research Group at the Faculty of Mechanical Engineering and Computer Science and has a goal to gather and share the knowledge of mechanics and machine building, automation and robotics, and many other related fields.
During the conference, our managing director, Paweł Wróbel, will lead a speech entitled: “How virtual reality helps automation start-ups”. His speech is scheduled for 11:10am.
We would like to invite you to participate in this event!
For more information, conference program and a live stream link, please visit: https://engineerxxi.ubb.edu.pl/en/
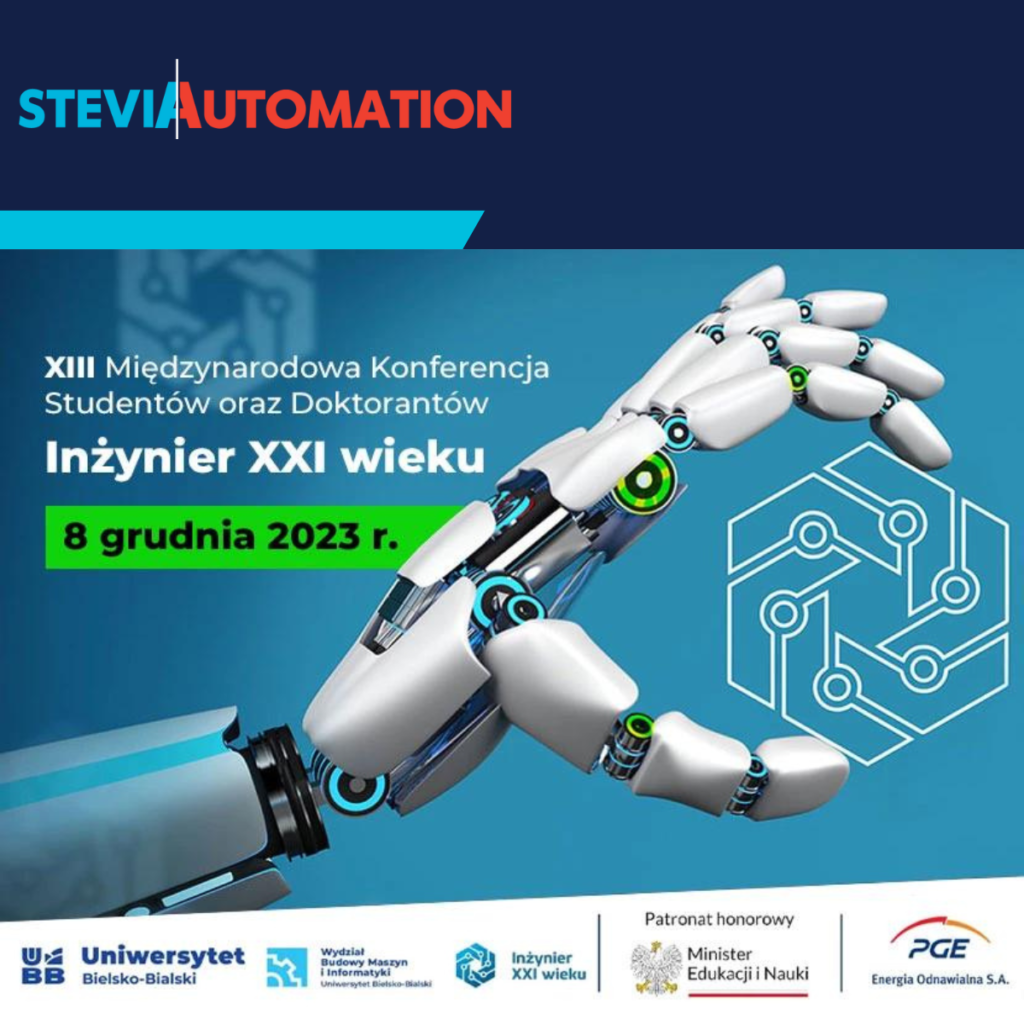
New employee on board!
30.11.2023
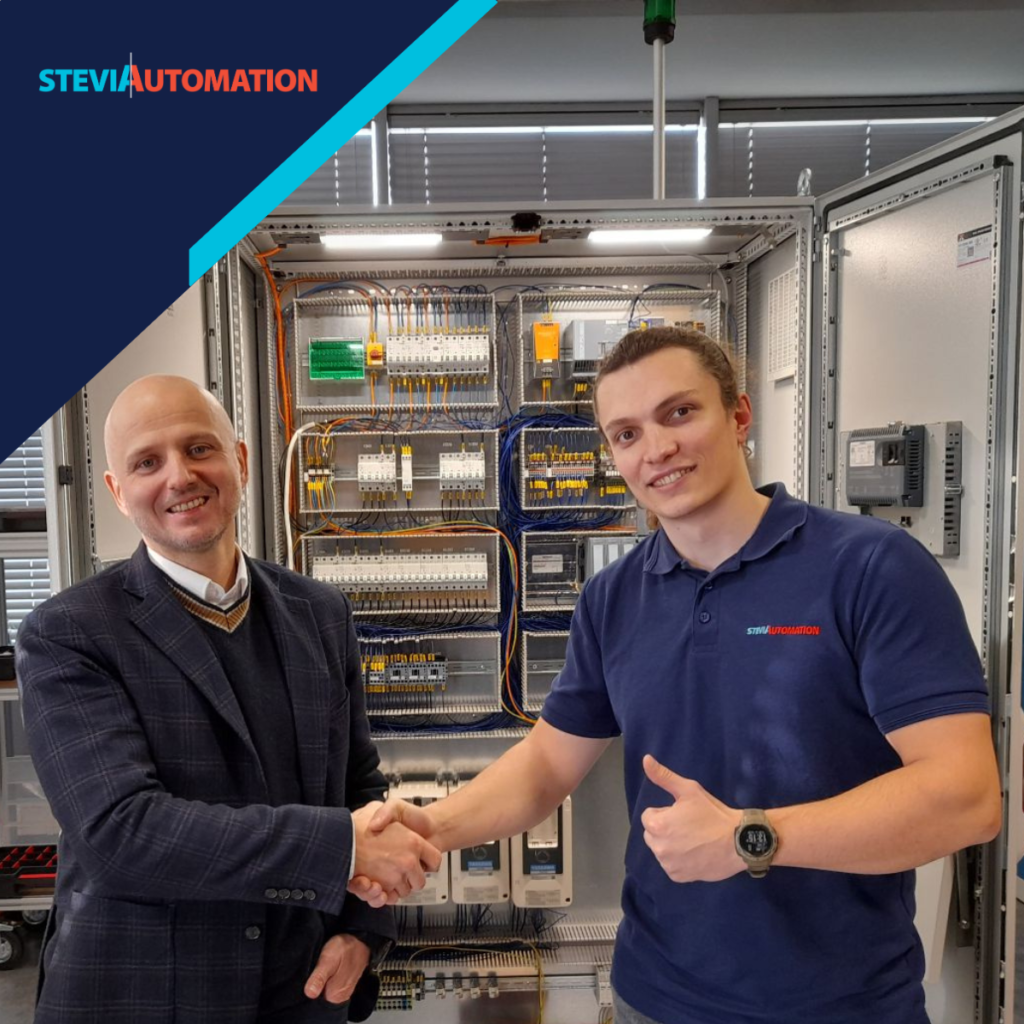
We are happy to inform that we have recently welcomed new PLC programmer, Arkadiusz, into our Katowice team.
Arkadiusz is an automation enthusiast, always focused on getting his tasks done neatly and efficiently. He is keen on searching for new development possibilities and constant improvement.
He is currently working on one of our projects in Germany and is already a vital part of our crew.
We wish Arek a lot of positive experiences, new achievements and good luck in his new position!
10 year anniversary of collaboration!
28.11.2023
Lately, Sit SteuerungsTechnik GmbH and Stevia Automation celebrated 10 years of cooperation. It all started in 2013 with two PLC programmers taking part in the first project. Over the years, the team has expanded to around 20 of them.
We are very thankful for this fruitful cooperation with our friends from Sit SteuerungsTechnik GmbH. It is a pleasure to work together with such professionals. We look forward to future projects!
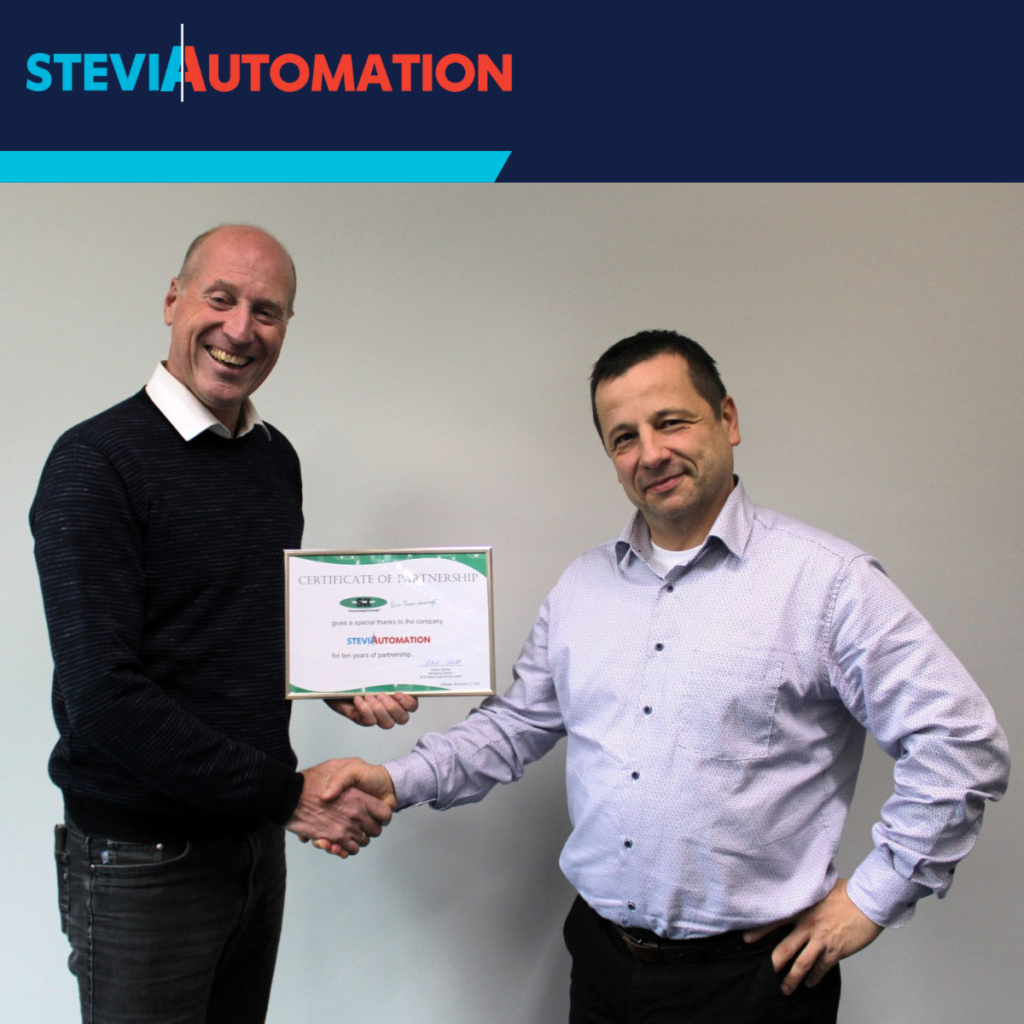
“50 Insiders on the Future of Intralogistics” is now live!
16.11.2023
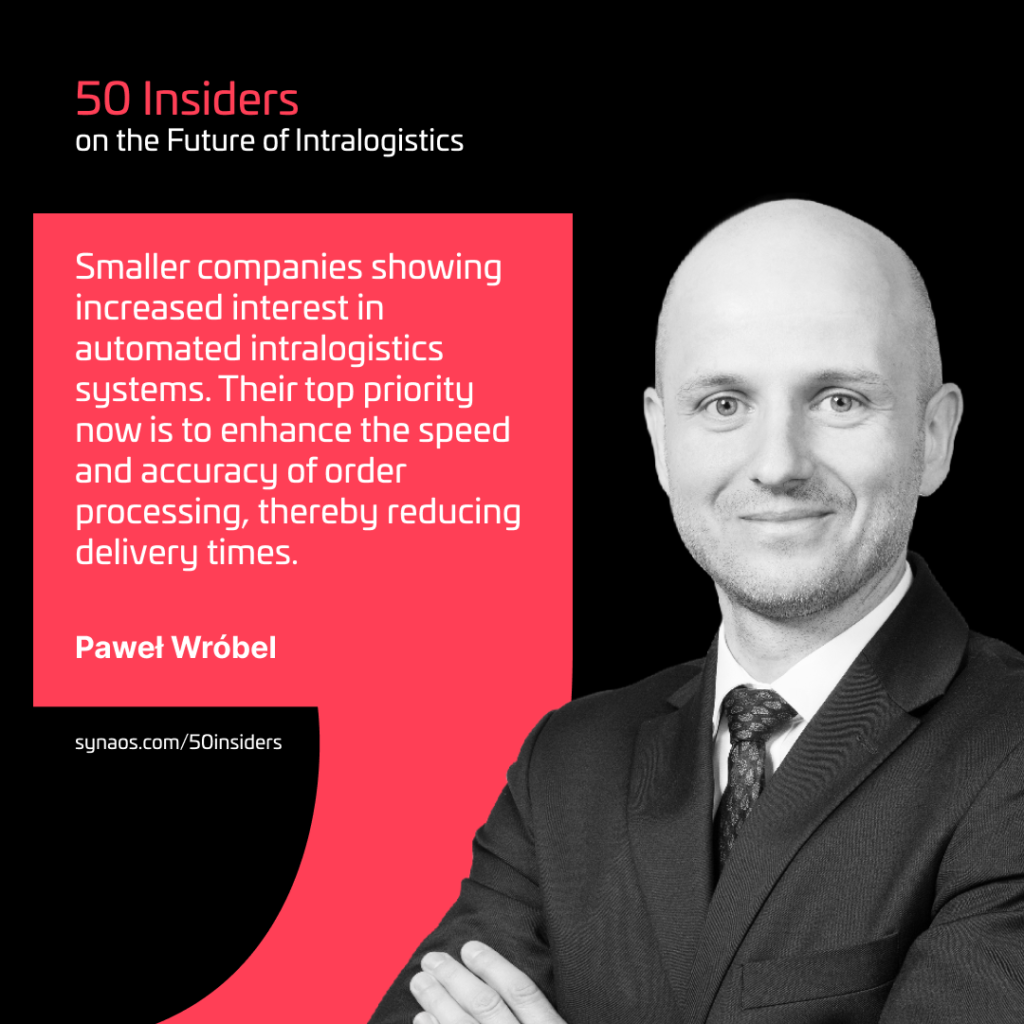
We are so excited to be a part of the report “50 Insiders on the Future of Intralogistics” created by Synaos, which went live yesterday!
It contains thoughts and opinions of 50 representatives from various companies in our industry. Our insight – “Hesitant to automate? Automation as a Service lowers Barriers”, located at page 81, is a statement of our Managing Director, Paweł Wróbel
We strongly encourage you to read this valuable report, as it describes the future of intralogistics from different perspectives, and is a knowledge compendium when it comes to current trends in the industry.
Please download the report here: https://eu1.hubs.ly/H065_Zj0
A big thank you to Mael Roth for giving us the opportunity to share our thoughts!
The Impact of Emulation on Project Work
07.11.2023
Virtual commissioning is highly beneficial for project work. By allowing the testing of a real project in a virtual environment before going to the actual site, project work can be significantly accelerated.
The system also facilitates programming work and reduces commissioning costs. Through the use of Emulate, a programmer can easily refine the PLC program, knowing that this emulation has a one-to-one reflection in reality. In the early stages, it’s also possible to detect any errors and shortcomings in the project and make corrections.
There are numerous advantages to using the Emulate program during project work. For the programmer, Emulate offers the opportunity to test the written program under real conditions and tailor the program to the device’s operation. In case of system errors, they can be swiftly eliminated with just a few clicks. Having a bird’s-eye view of the entire long assembly line allows for quicker error detection compared to searching for issues on long, often hundreds of meters, installations. For project creators, it is highly useful that the project can be assessed and improved to work perfectly through emulation.
The use of Emulate reduces the startup time of the system on-site because most errors are eliminated during office testing. This also translates to a reduction in expenses related to real tests on-site, as physical tests at the site typically involve a significant number of personnel. Physical tests on-site are usually challenging and time-consuming due to the fact that many installations are located in hard-to-reach places, such as high ceilings in industrial halls.
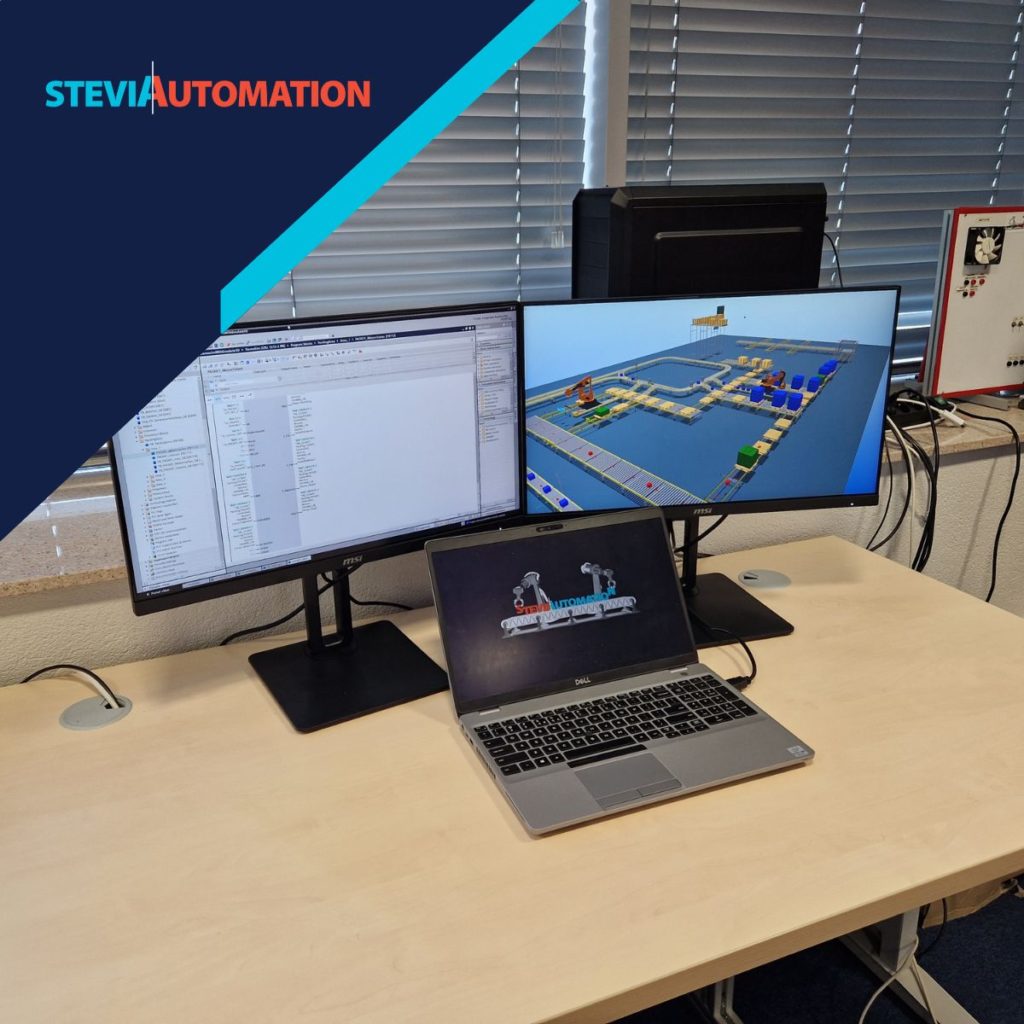
Project: Automated parcel sorter
24.10.2023
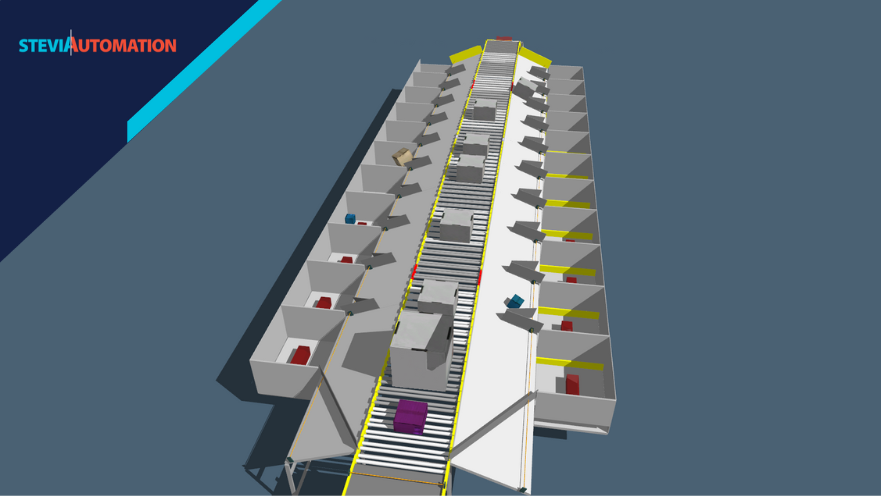
Currently we are working on a project, whose purpose is automated parcel sorting. During this project, our scope is the whole electrical preparation, which includes EPLAN, control cabinets prefabrication and its on-site installation, as well as the PLC and HMI programming.
The essence of this project is programming and commissioning of an automated sorter, whose task is to transport parcels to their respective destinations, where order assembly takes place, before they are shipped to specific locations.
The sorter contains 14 induction points, and 23 chutes. A parcel, placed at one of the induction points, makes its way out to the scanning station. The scanning tunnel, added on to the sorter, is able to scan the package’s code, no matter which side of the package it is situated at.
Additionally, the scanning tunnel has a feature of an automatic dimensioning of each package, and is able to take a photograph of it. The collected data about the packages are then saved in the WMS system, so that the details of each one are available to system operators.
We are happy we can realize another exciting project!
Real possibilities of virtual commissioning
12.10.2023
The electrical-mechanical concept of a project is usually outlined before the Emulate system is applied. This program can also assist in the conceptual stage, where changes to the project can be made and the final appearance of the installation can be determined. The system allows for testing individual project elements to ensure that the required performance can be achieved with the selected mechanical components. Thanks to the virtual commissioning system, a project can transition from the conceptual stage to the execution stage much more quickly.
Using the Emulate program, you can define parameters for the designed system, such as its operating speed and throughput, for example, how many packages will pass through the machine per minute. In the initial stages of creating the model, even the smallest errors in the concept or project documentation can be detected. It’s worth emphasizing that you can see precise real parameters without the need for actual physical setup.
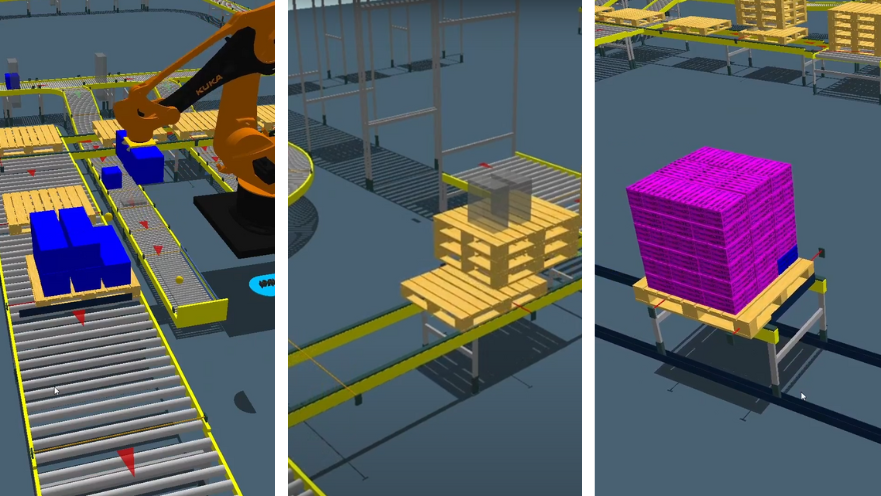
Objects in the Emulate visualization have declared coefficients, such as friction, allowing the visualization to be entirely consistent with the laws of physics. The visualization can show things like the inertia of elements, the realistic behavior of elements during flow, including real-time stopping, and the movement of elements at the same speed as on a real machine. The entire system’s operation process is visible while adhering to the laws of physics.
With Emulate, you can also create simulations of non-standard elements, different from standard roller sorters or conveyor systems. Emulate allows you to visualize industrial robots or elevators with all their features and functions just like in reality. Visualization can also involve automated transfer cars, used for moving large and heavy items through production halls. Interesting examples of emulation applications include visualizing a pallet wrapper, spiral conveyors, or stackers that automatically stack goods.
Getting close to success!
02.10.2023
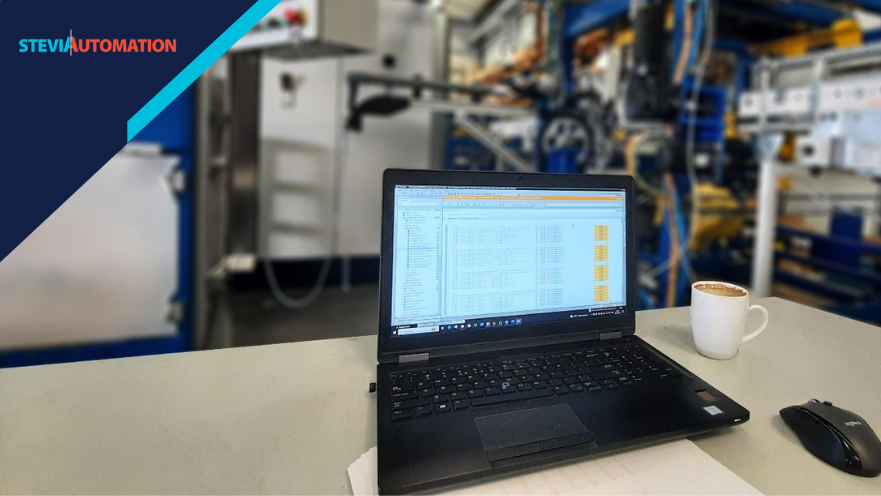
Lately, our team has been working on the commissioning of the wheel balancing machine at our client’s location abroad. Our scope includes the electrical designing and installation, PLC and robot programming, as well as commissioning.
While we are completing the work, we are happy that we can contribute to the success of our client, through our knowledge and experience. The commissioning part of the project often brings many challenges, however we are always ready to take them up and deliver the best service we can.
We are also looking forward to many new projects coming!
How does virtual commissioning work?
19.09.2023
To create a virtual commissioning, a library of components is primarily needed, such as conveyors, elevators, curves, and diverts. These components are assembled like building blocks to construct the designed object. The component library can be modified or expanded. You can create and program a new element that is not a part of the standard library and implement it into the emulation.
When assembling the designed model, the designer sets parameters for each element from the library. These parameters may include things like speed, conveyor material type, or friction. The Emulate 3D program allows for configuring virtual system elements according to the specifications of real devices in the project.
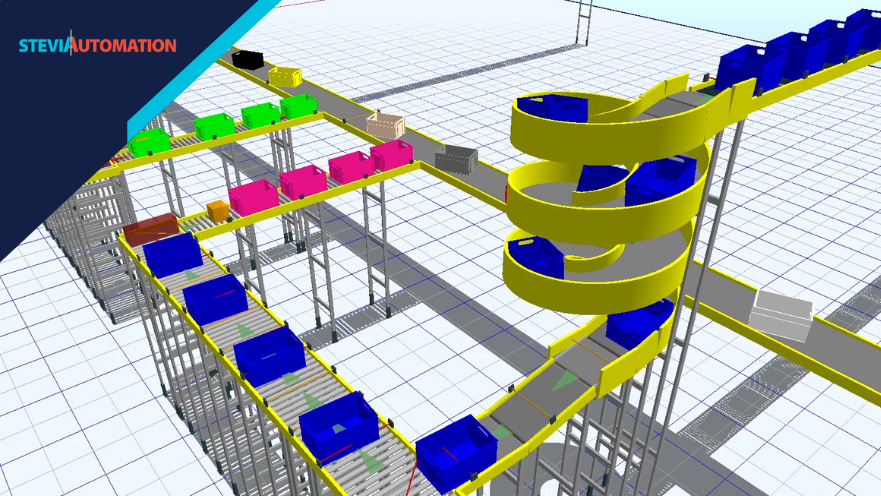
Virtual commissioning relies on connecting a real controller to the emulation. The PLC controller sees the devices and can control them long before the actual on-site installation. The programmer observes the control effects on the virtual model of the system.
A crucial integration component between the Emulate 3D program and real devices is TwinCat. It is a separate program installed to enable communication between the Emulate 3D program, the PLC controller and the SCADA system. The programmer uploads the program to the controller and through TwinCat, the controller communicates with the virtual model, allowing for system testing.
The translator between the Emulate environment and the PLC controller is a configuration list. This is often an Excel file that contains bindings of variables present in the controller and in the emulation.
Virtual commissioning and its advantages
29.08.2023
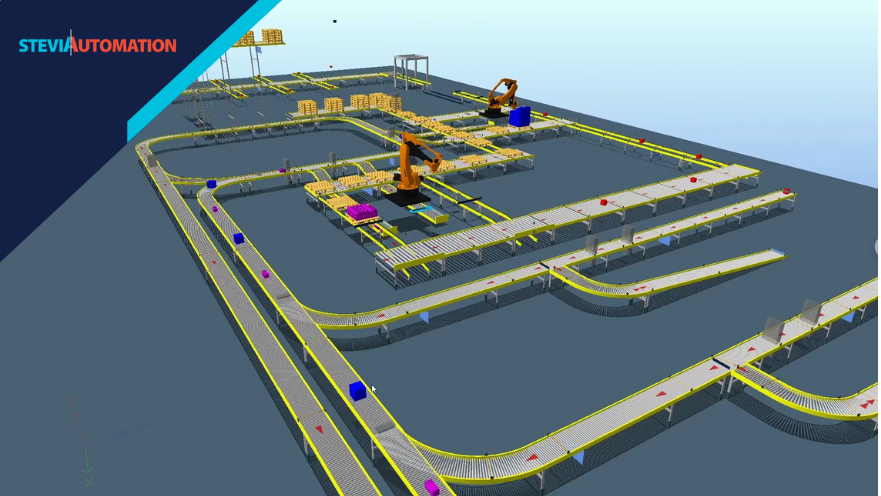
In many ways, the virtual commissioning (Emulate 3D) contributes towards the success of our projects.
It allows for viewing and testing the concept of the project before the real-life commissioning phase. It also enables our engineers to detect and correct errors and shortcomings of the software, which makes their job more efficient.
Our engineers create the virtual model of the exactly the same system as in the project, so that the mechanical construction as well as its software can be tested.
For our clients, it is a good opportunity to see the test version of the project and its impact on the company’s processes, it also helps the client to point out any elements that need modifications. Using virtual commissioning, we can select the version of the project that fits our customers’ needs the most and make sure that the project is 100% technically correct.
“The Active Five” is in the books!
17.08.2023
Last Sunday, our team completed yet another running challenge – “The Active Five”. It was a 5 kilometer run, which took place in Studzienice, a Siesian village located not far from the city of Katowice.
We had to face an intense summer heat, which made running quite tough that day. The water sprays that were set up by locals on the road were more than helpful.
Despite the strenuous conditions, all of the team members managed to finish the run in less than 30 minute time!
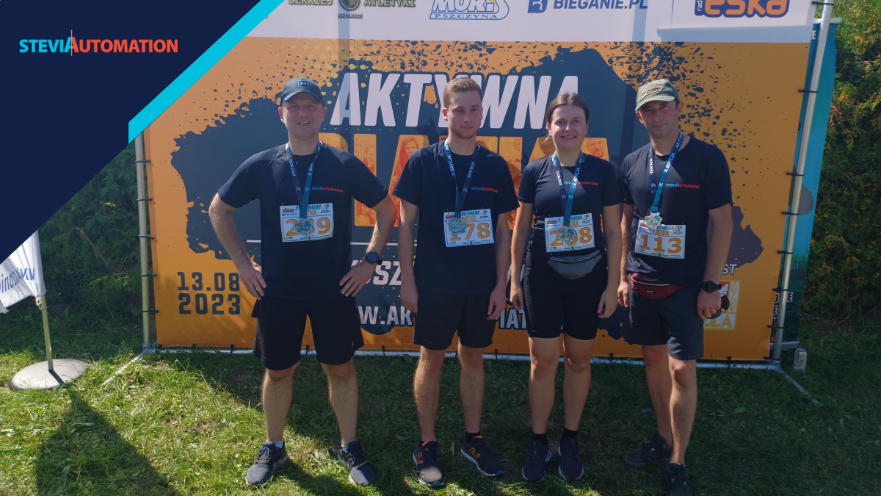
Inside our workshop #3
08.08.2023
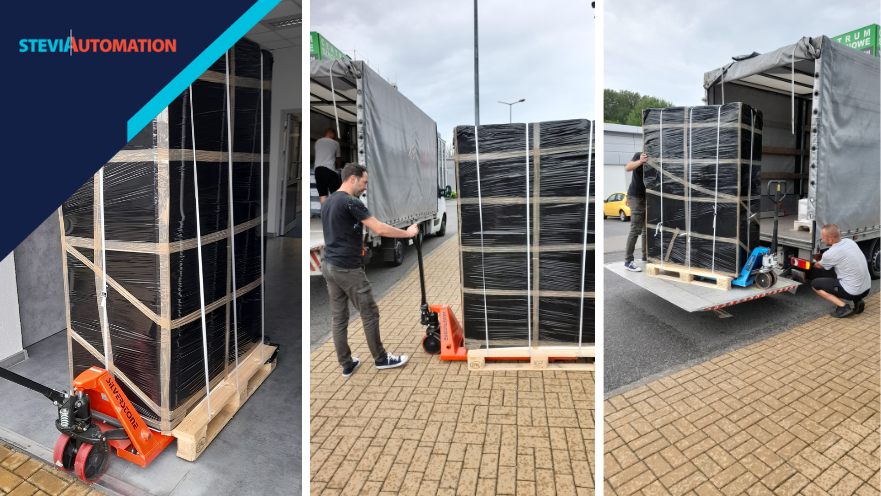
The control cabinets we’ve been working on, as well as their additional equipment were packed, and loaded into a vehicle. The transportation will last a couple of days to deliver the goods to our client in Germany.
We made sure the transported cabinets were safely packed, preventing the goods from any damage. We are looking forward to our packages to be delivered, and we are happy to begin the next – commissioning chapter of this project!
Inside our workshop #2
01.08.2023
Our prepared control cabinets are going to leave the workshop very soon. Due to this fact, we perform complete measurements and tests to make sure they are fully safe and ready for further stages of the project.
The cabinets are always produced according to valid standards and are given a CE certificate. The tests ended successfully and the cabinets will be with our client shortly 🙂
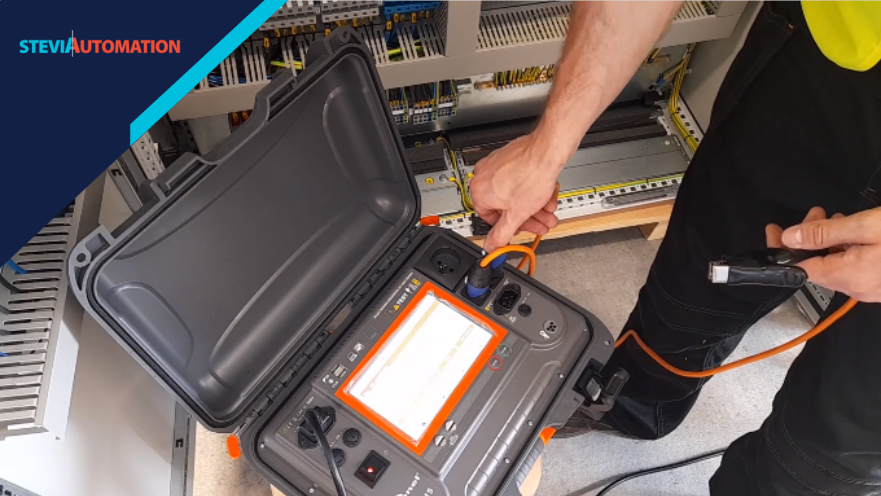
Inside our workshop #1
20.07.2023
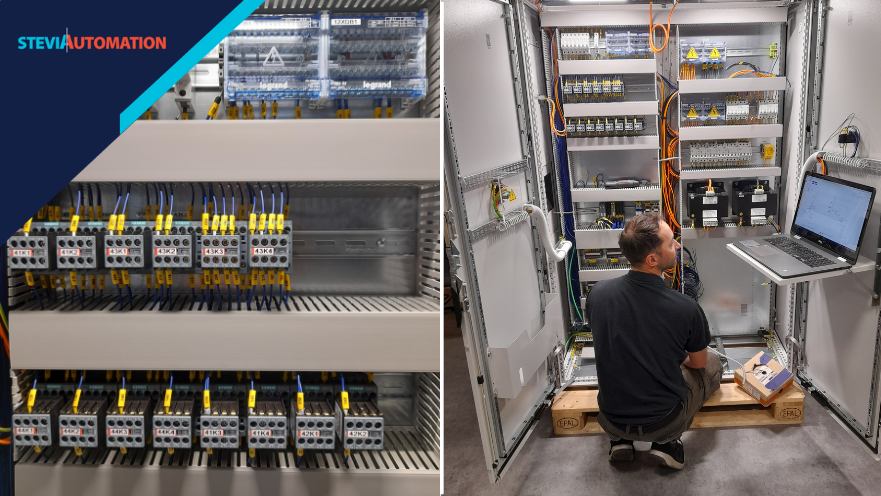
Currently, we are working on completing another project for the international provider in the automotive industry.
The project – control system for an automated wheel balancing machine – includes electrical designing, control cabinets prefabrication, on-site electrical installation and PLC & robot programming. We also perform a full commissioning and configuration of the system, connected with monitoring and support during the first phase of production.
One of the very important steps here is the prefabrication of the control cabinet. Our cabinets contain the best quality components, that are carefully assorted for the need of every project.
As a result, adding the new machines makes the whole production process faster and more precise, which gives the end user way better efficiency. We are glad we are able to provide the needed service and support to our client.
New employee on board!
29.06.2023
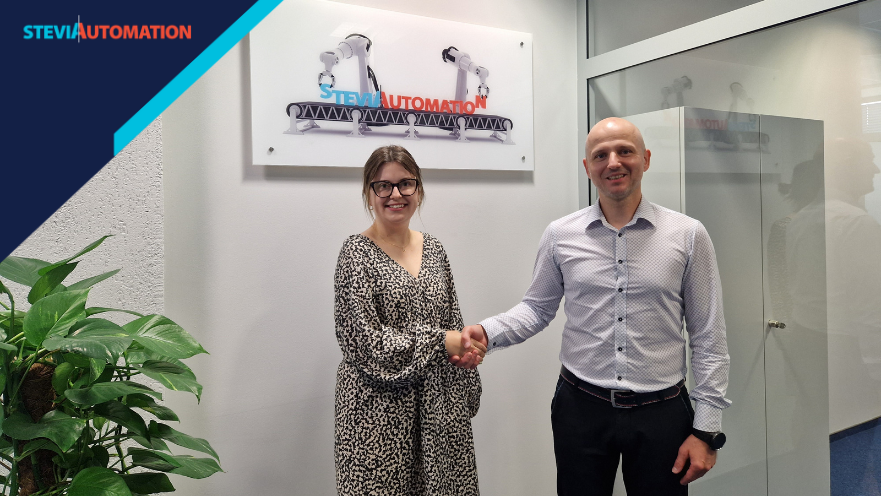
This month, our company gained a new team member, Sylwia, who took the position of Administrative Assistant.
Sylwia will be taking care of main organizational affairs of the Katowice office, as well as employee related tasks and company purchases.
She is looking forward to using her skills and knowledge to complete designated tasks in the best way possible.
We are excited to welcome her in our team and we wish her a lot of great achievements in her new role!
The Firefly Run is finished!
20.06.2023
Last Saturday our team participated in the “VIII Firefly Run of Siemianowice”, which is organized annually to celebrate the upcoming summer time of the year.
It was a great opportunity for all the colleagues to integrate and have fun after work, with a little bit of sport rivalry mixed in.
We are happy to announce that all of the team successfully reached the finish line, and we wish them all the best in the future running challenges 🙂
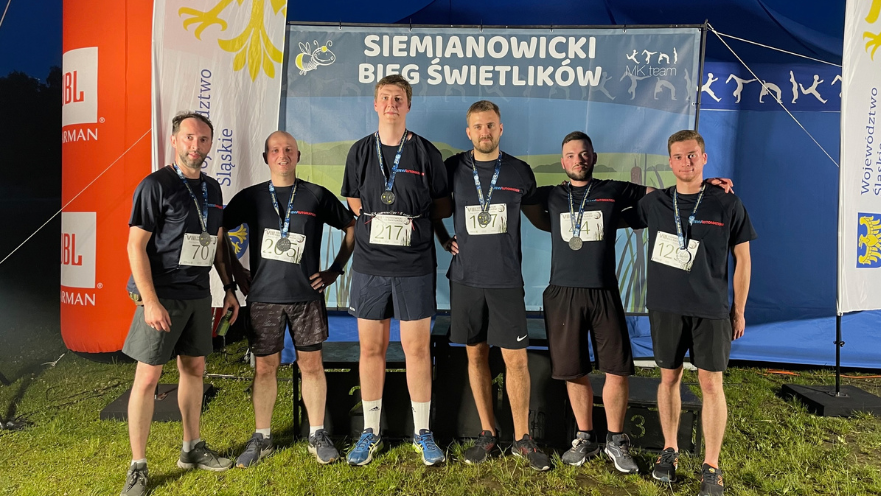
Advantages of the scanning tunnel
23.05.2023
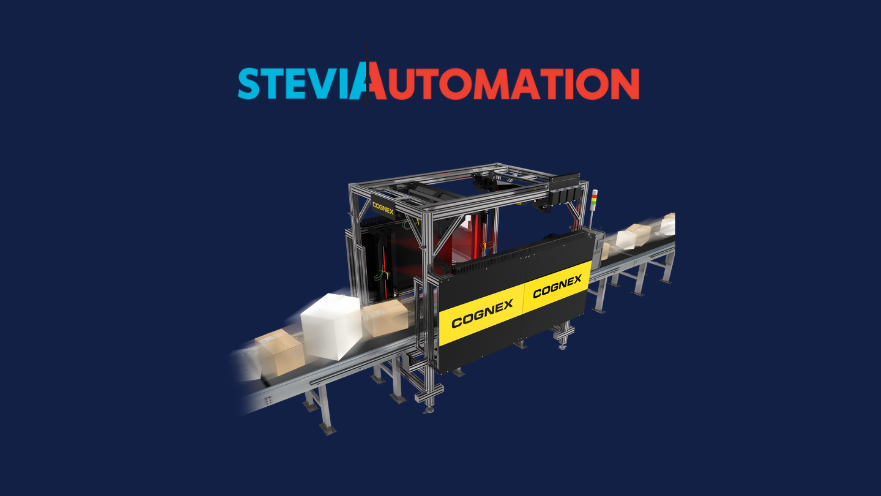
When carrying out our projects in the area of intralogistics, in situations where we do not have a precisely defined label position, we use a scanning tunnel. The system allows for reading the package from multiple sides, depending on the configuration, and transmitting the information to the control system.
The use of cameras in the tunnel enables:
- the ability to read the label from any side of the package,
- the ability to measure the package dimensions,
- information about the precise position of the package on the conveyor,
- taking the picture and transferring it to the database,
- increased efficiency of package throughput.
The scanning tunnel allows for reading codes from packages of various shapes and sizes, from large cartons to small envelopes, for example.
LogiMAT fair is behind us
09.05.2023
We can certainly say that it was a fruitful time full of interesting conversations.
We are happy that we participated in this event for another year and were able to exchange our industry experiences with so many automation and intralogistics enthusiasts.
Meanwhile, we are returning to work and getting in touch with the people we met.
See you next year!
Let’s meet in Stuttgart!
18.04.2023
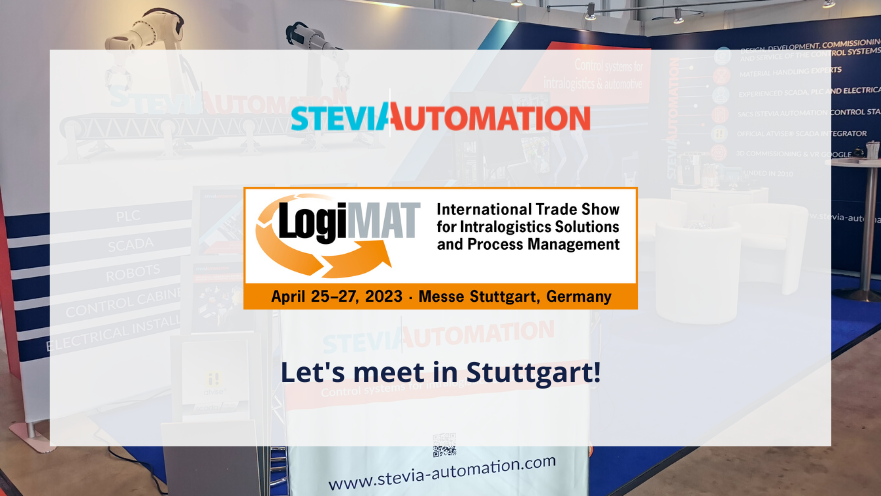
Only a few days left until the LogiMAT International Trade Show in Stuttgart.
We are excited to have the opportunity to talk to you in person.
If you are interested in how we can assist you in selecting and implementing suitable control systems for your requirements, please visit us at booth number 5F51 in hall number 5 and speak with us.
Come visit our booth at the largest intralogistics trade fair in Europe!
Safety in automation systems
30.03.2023
Safety in automation systems is a crucial issue. In the control systems we implement, we take into account all the requirements of the Machinery Directive and harmonised standards. When designing safety circuits, we only rely on components from reliable manufacturers.
Every time before we begin the implementation stage, we evaluate the designed safety functions according to ISO 13849-1 standard. For this purpose, we use dedicated SISTEMA software. The calculations we perform assure us that the control system will achieve the required Performance Level (PLr).
For us, there are no exceptions – our control system must be reliable and prevent any potential threat. We must be sure that the machine we deliver to our client is fully safe.
Let’s meet at the LogiMAT fair
09.03.2023
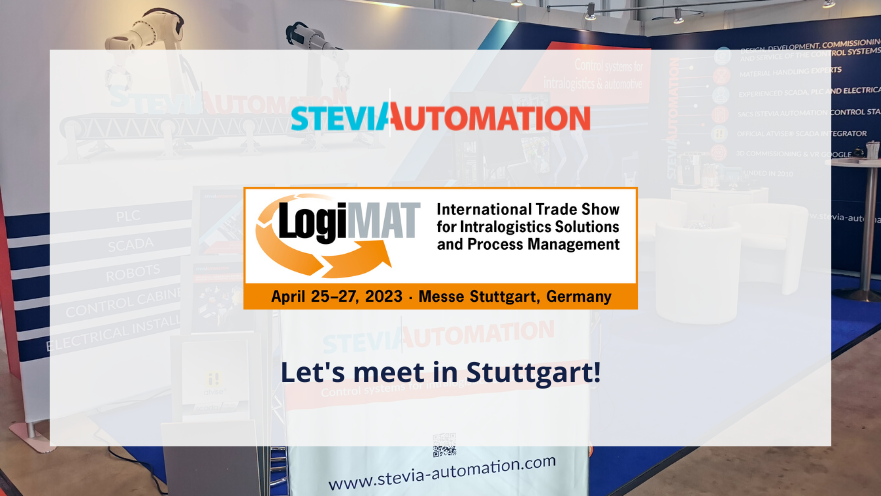
The biggest intralogistics trade show – LogiMAT is coming soon.
We’re happy to inform you that we will be at this event again. We’re sure that it will be a perfect opportunity to meet and speak to each other. To talk about the best solutions and meet new customers.
We’re looking forward to these days and already invite you to hall 5 on stand 5F51!
An article by our employee in a scientific journal
23.02.2023
The key to success are good specialists.
We know about that, that’s why we employ the best experts.
Recently an article by one of our employees was published in a scientific journal.
Eryk wrote how the line optimization looks like. He listed each step and wrote the advantages of each solution. He showed how to perform work in the most satisfactory way for the client and how to minimize the risk of possible errors.
We’re happy that we create a space, where our employees can develop.
We encourage you to read!
http://www.astrj.com/Author-Eryk-Gawron/214027
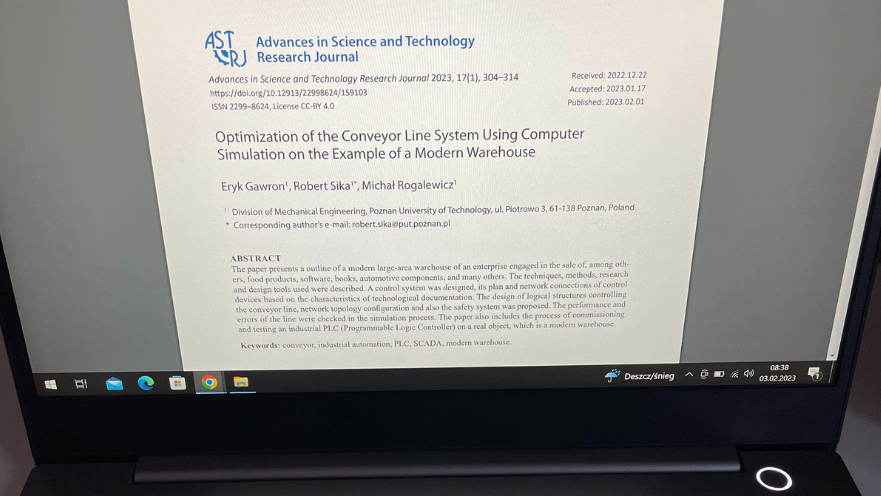
We are commissioning another warehouse in the UK
09.02.2023
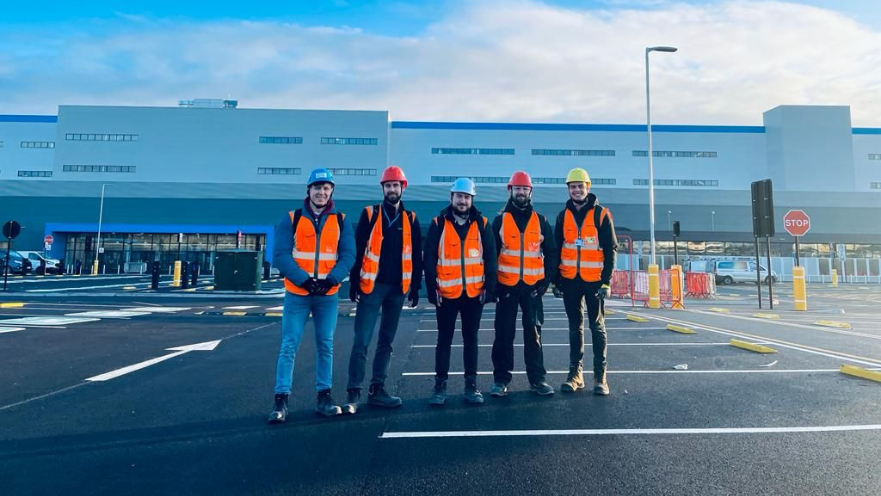
Our team is performing tests of programmed lines. We are commissioning an advanced sort control system. It includes product transport and sorting. Our programming works include an advanced tracking system and integration with WMS.
System will help to reduce lead time and maximize performance of the internal delivery system. We carry out all works on time, ensuring the solid performance of each element. If you would like to learn more about what solutions we have delivered to our customers go here
KPI – increase efficiency and optimize processes
24.01.2023
The logistics and automotive sectors generate a huge amount of data. An effective way to use them is the definition of key performance indicators – KPI (Key Performance Indicator), which are used to measure the degree of achievement of the organization’s goals.
In practice, depending on the analyzed object, various indicators are selected, such as total equipment effectiveness – OEE (Overall Equipment Effectiveness), work efficiency, order fulfillment time or MTTR (Mean Time To Repair).
Well-designed performance metrics allow you to quantify the performance of individual employees, lines, departments and plants.
When defining indicators, it is extremely important to focus on a few key parameters so that too many of them do not obscure the picture. The selected KPIs should take into account the most important processes/functional areas of the company.
The task seems simple, but only seemingly, because it is based on both knowledge and experience. We are happy to share our experience on this topic. Write to us – contact@stevia-automation.pl
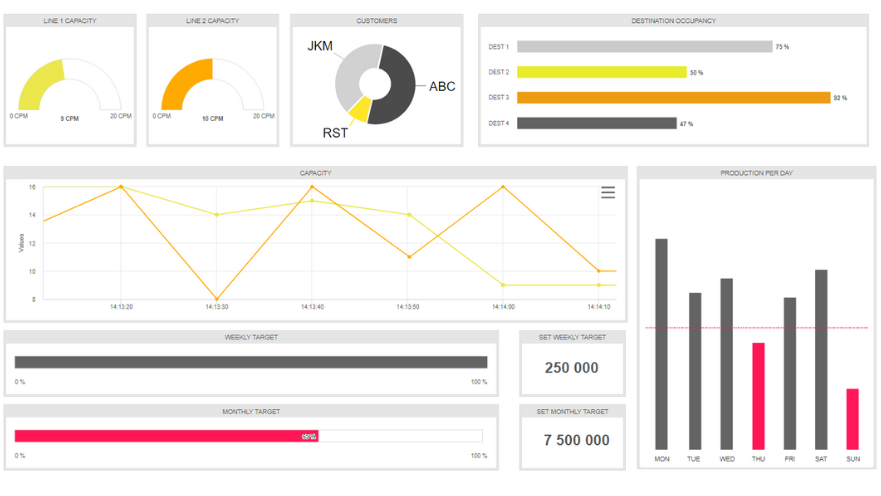
It was a good year!
05.01.2023
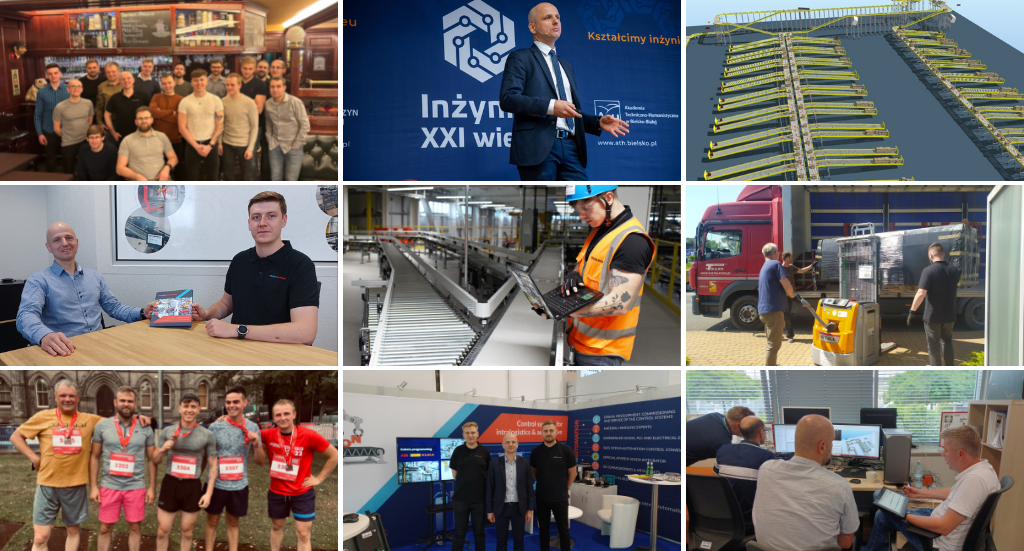
The intensive year is behind us. It was a time full of changes, successes and new experiences.
We’re proud because all of our 21 (bigger and smaller) projects were completed on time. For the next time we worked for global companies and every customer was satisfied with the system we’ve provided.
Paweł Wróbel joined our team in Katowice. Thanks to this our Katowice branch started to develop intensively.
Our first visit to Logimat in Stuttgart was also very successful because of the new business opportunities we found there.
We’re happy because we’ve got very committed and skillful employees and we know that we could do nothing without them.
2023 is ahead of us, full of challenges and interesting projects for which we are ready.
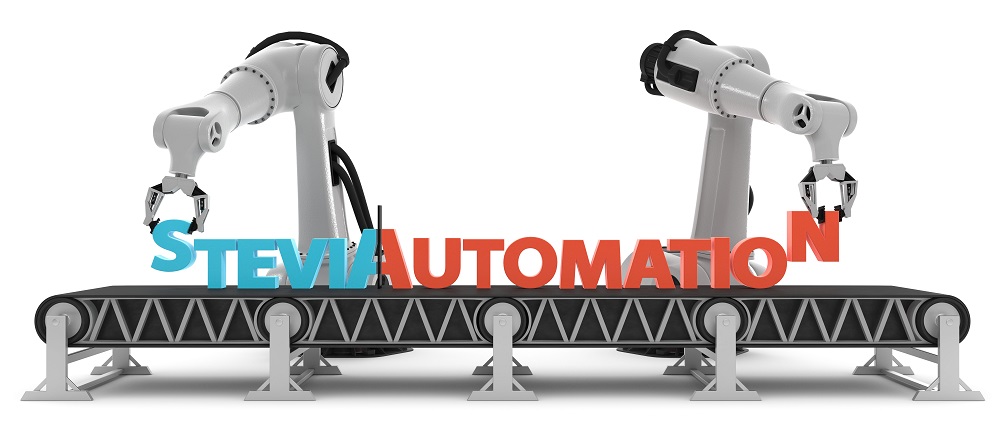