Throughout our more than 15 years of operation, we have earned a reputation as specialists in the field of automation systems integration. When carrying out warehouse or production system automation projects, we are responsible for designing and implementing advanced control systems. Our work contributes to the integration and synchronization of hardware and software into a unified, interoperable system. What are the benefits of working with a systems integrator? Read on to find out.
Stevia Automation – Your industrial automation systems integrator
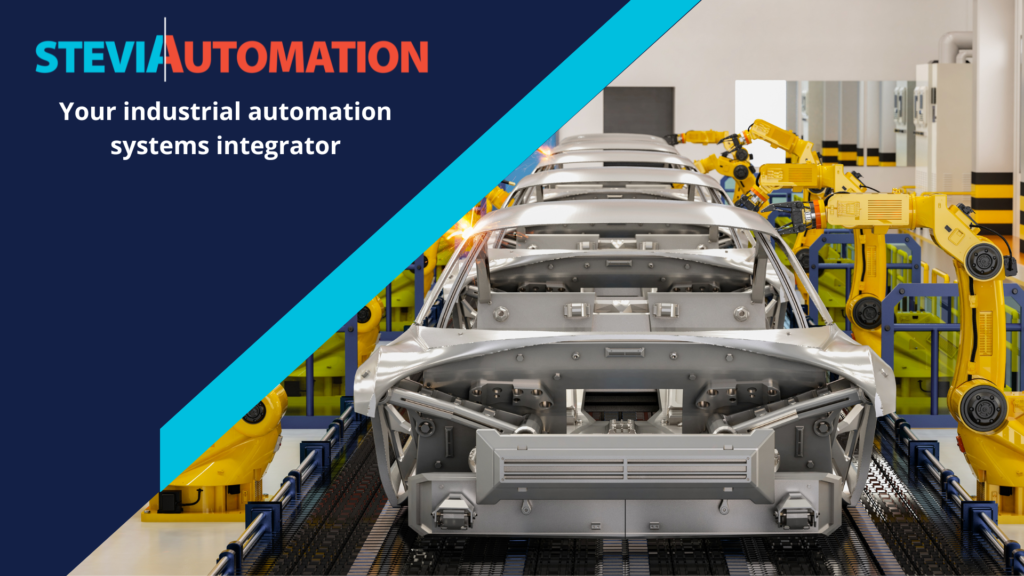
What does our work as an industrial automation systems integrator look like?
Our work as an industrial automation systems integrator begins as early as the conceptual phase of the project. Our engineers identify and assess the client’s needs in order to select the appropriate resources and type of services to be provided. Once the project is approved, the automation systems integrator physically installs the devices, programs PLCs, configures visualization systems, and connects new components with higher-level systems such as SCADA.
An integrator can provide services not only at the beginning of the automation journey but also during the expansion and further development of an automated system at a given facility. In our projects, we offer services including PLC programming, electrical design in EPLAN, commissioning, and post-commissioning support.
The work of an industrial automation systems integrator involves overseeing the project throughout all its phases—from selecting the right concept and defining project activities, to post-commissioning testing, staff training, and ongoing service support during the system’s operational life.
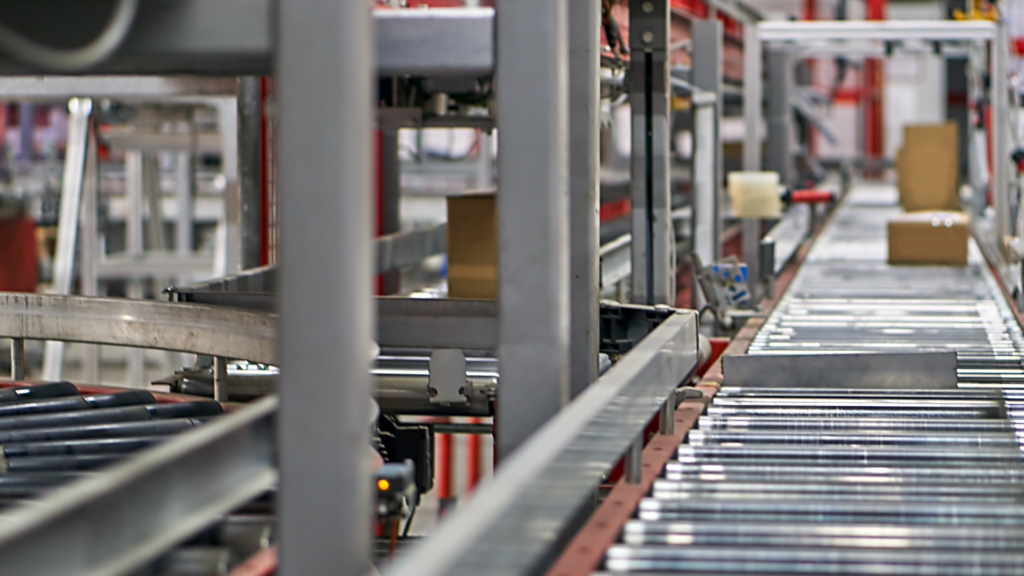
Integration vs. Automation of Industrial Systems
The integration of machines with control systems can be considered one of the foundations of automation. This type of integration occurs both when a company plans to modernize its existing machinery and equipment, as well as when implementing new automation solutions within a facility. Every new machine in a production or warehouse system must be integrated with the IT system to enable efficient automated goods flow and identification.
The automated industrial systems we most often work with are characterized by a high degree of process repeatability. These include operations such as logistics, and production in the food, chemical, and automotive industries. In such environments, automation is continuously expanding to meet the growing demand for fast product delivery.
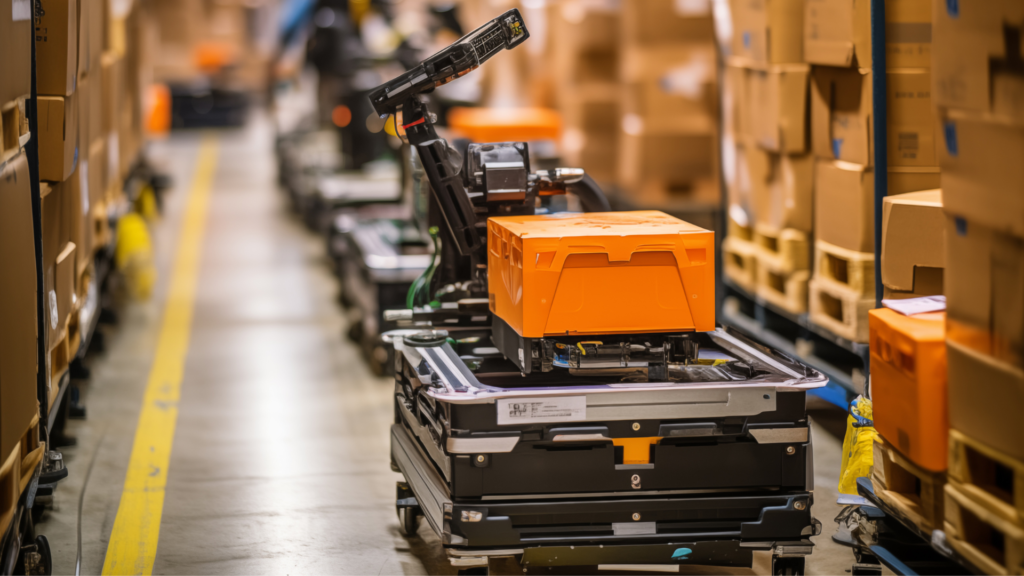
How to recognize the need to choose your industrial automation systems integrator?
The need for ongoing cooperation with a control systems integrator arises when multiple types of modern technologies are used within a single facility, and when complex processes require numerous automated systems. The integrator oversees the proper functioning of these systems and assists in selecting new concepts.
Working with an integrator results in greater process stability, improved control, and compliance with all applicable technical standards and safety regulations. By establishing such a partnership, a business ensures flexibility in implementing customized solutions and gains access to continuous support for the implemented systems.
As an experienced control systems integrator, we invite you to get in touch. Our engineers will gladly assess the condition and sophistication of your automated systems and assist in selecting concepts for automation expansion.